WORDS & PHOTOS • SAM TAGGART
For Atomic, product design and development doesn’t stop with skis. Committed to advancing the sport in every way, the heritage brand also centralizes its hardgoods programs—think: boots, helmets and goggles—at its headquarters in Altenmarkt, just steps from its factory, in the heart of the Austrian Alps. In this special feature story, we’re taking a look beyond the The Hills Are Alive article featured in FREESKIER’s Resort Guide (22.2), diving deeper into the products and the people who make them come to life. Below, you’ll find a conversation with Matt Manser, an ex-pat Vermonter and the global product manager of alpine and touring boots at Atomic. Keep reading to get the full story of how Atomic’s Hawx Boot—a staple of its freeride-touring line for over a decade—has evolved into one of the lightest, stiffest ski-touring boots available, as well as boot fitting advice and insights from Manser’s fifteen-plus years of experience in the field.
There are many philosophies that make a great ski boot, what are some of the principles that Atomic sticks to during ski boot development?
What we think are really at the core of every boot… is fit, comfort, and performance. These three things really encapsulate all of our R&D [research and development] concerns and focus in the ski boot world. Obviously, if you look at what a World Cup Racer defines as fit, comfort, performance it’s really different from someone who skis five days a year. It’s important to look at the needs of each consumer—how they define fit, how they define comfort, how they define performance—and come up with the solutions to meet those needs.
How have you stayed true to those practices in your boot collection for this winter season?
The main boot we should talk about is new Hawx Ultra XTD. It has some major updates in terms of fit, comfort and performance, geared towards that freeride-touring consumer… they’re in the resort, they’re in the backcountry and they’re in the side-country, and [these consumers] want one boot to rule them all. With the first iteration of the Ultra XTD, we really hit it out of the park… but the main thing new for this year’s boot is that we’ve included a brand new liner from the ground-up. It’s an all new fit, all new level of comfort, cushioning and performance. We wanted to keep it lightweight and touring-friendly, but make it more resort-friendly at the same time. So, this boot has a much more anatomical fit in the heel and ankle area and is much more supportive, much firmer. We’ve [also] included a plastic insert in the front of the tongue, to help drive power to the ski and take up more shock absorption and cushioning.
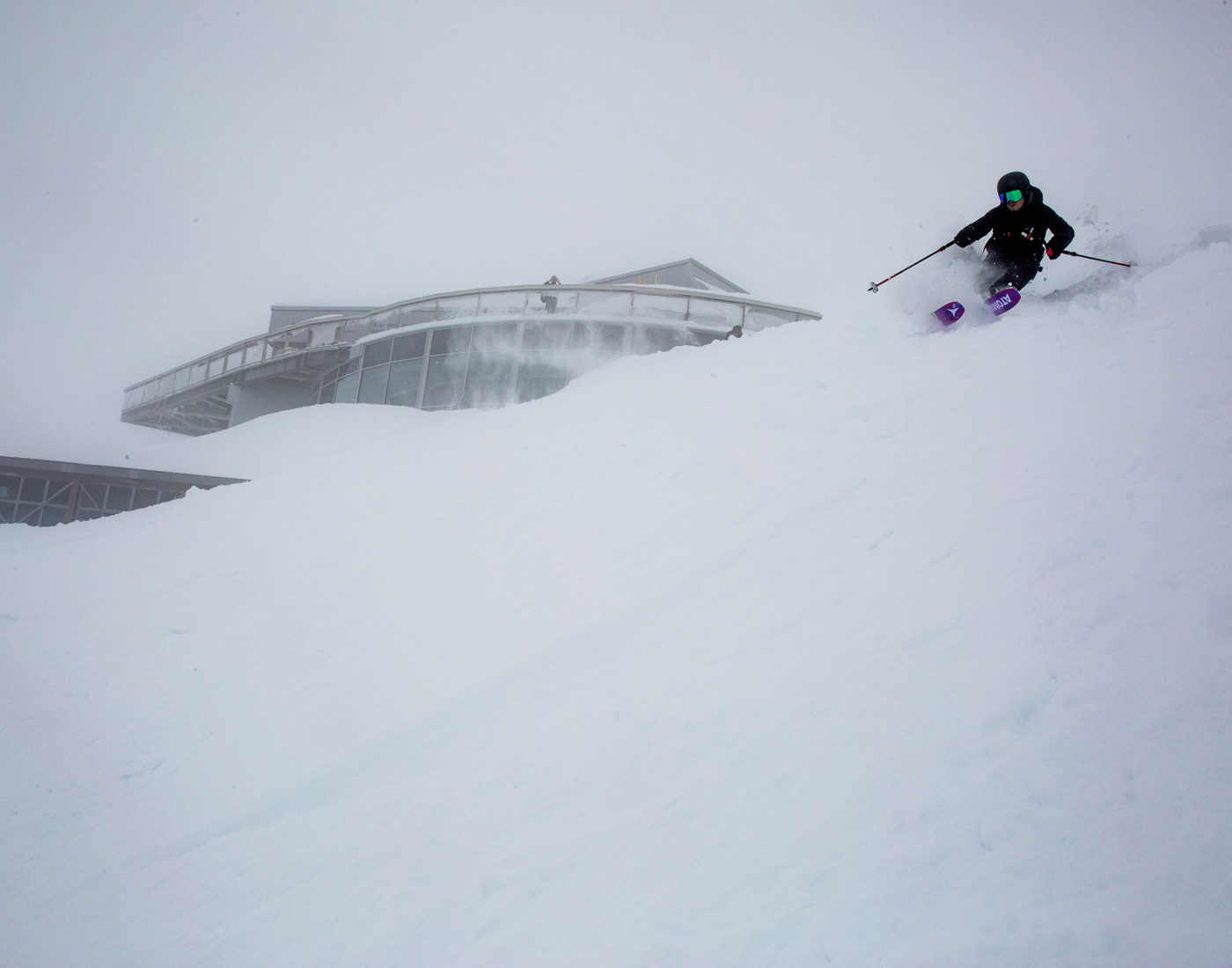
The Hawx line has been in Atomic’s repertoire for awhile. What has been the progression and how did we end up here with the new Hawx Ultra XTD boots?
Hawx, as a general boot concept, started about 2007. What really made Hawx famous and why it took off so well was that it was one of the first boots to really blend a high degree of foothold and awesome comfort, all in one package. At that stage in the evolution of boots, you kinda had to pick one or the other: You either had super cushiony boots, or you had race boots. The Hawx, and its original formation, really walked the line of having both foothold and comfort, all roped into one.
At first, it was only produced at a 100 millimeter last, so a medium fit, average volume style of boot, which fit a lot of people—and it’s what helped take it to being the most sold boot in the USA in its first couple years. Eventually we started to realize a medium-fitting boot is awesome, but there are people that want a more narrow fit and a wide fit, too; that’s where you saw the evolution of the Hawx unfold over the next few years. We launched a medium fit to replace the original and then also a new wide fit and a narrow fit. Then, the evolution of the Backland boot really started to catapult us into this lightweight mindset—the idea that lightweight boots could ski well.
We started to look at alpine boots in a completely different angle at that point; this is where idea of bringing Atomic’s Prolite technology into ski boots came from. We were skiing the first prototypes of the Backland boots… and we were really surprised at how well [they] skied. All the lights started going off in our heads, and that’s really where the first Hawx Ultra was born. The first prototypes of that boot were interesting: We made it a little too light at first and it wasn’t giving us the skiing performance that we wanted. We really started to look at every aspect of the lower shell, the cuff, [and] where we needed to add more material; at the same time, [we looked for] where we could remove material to keep it lightweight but still deliver the skiing performance that an alpine boot should have.
Can you explain Atomic’s Prolite construction a bit more? What makes it so unique?
Prolite embodies the philosophy of making things light where it can be but supportive and strong enough where it has to be. That entire philosophy came about when we started to make the Backland series of touring boots. When you make a boot that weighs just one kilo [1,000 grams] in total, you really have to analyze every aspect of the lower shell, the liner and the cuff to make sure that they ski well. When we started to apply that concept to alpine boots—noticing where the hinge points start to bellow or the boots start to deform in ways that are detrimental to skiing performance—we have to add material to those zones to make sure the boot skis and behaves the way we want it to. The early challenges of that [development] were trying to figure out where exactly material was crucial, and where it could be removed without taking away the performance of the boot.
Were there any big roadblocks or difficulties you experienced while developing Prolite?
We had to actually invent entirely new mold production techniques to make it possible. Just simply making things “thin” isn’t really what has existed in the ski boot mold construction in the last thirty years; ski boots had been thick and heavy, they hadn’t really changed a whole lot. When we wanted to make an alpine boot mimic a touring boot—its construction and wall thickness—these mold techniques didn’t exist. We had to invent new ways to build ski boot molds from the ground-up and that was a big learning curve.
When it came time to go skiing on snow, we would realize we went a little too thin, a little too lightweight, in these first prototypes. We [had to go] back to the drawing board and add thickness in certain key spots to make sure the boot still skis properly. It’s how to walk that line between being super light but maintaining a real “ski boot” feel. One of the metaphors I like to draw upon when I am explaining this to people is: Have you ever seen a bike frame or bike tube that’s been cut in half? If you looked down a tube of a mountain bike or a road bike, you’d see its really thick in the areas where it joins into another tube, but then it thins out again in the middle where you can save weight. If you apply that kind of metaphor to a ski boot’s lower shell, you can quickly grasp what it is we try to do with the new Hawx Ultra XTD, and the Hawx family of boots, in general.
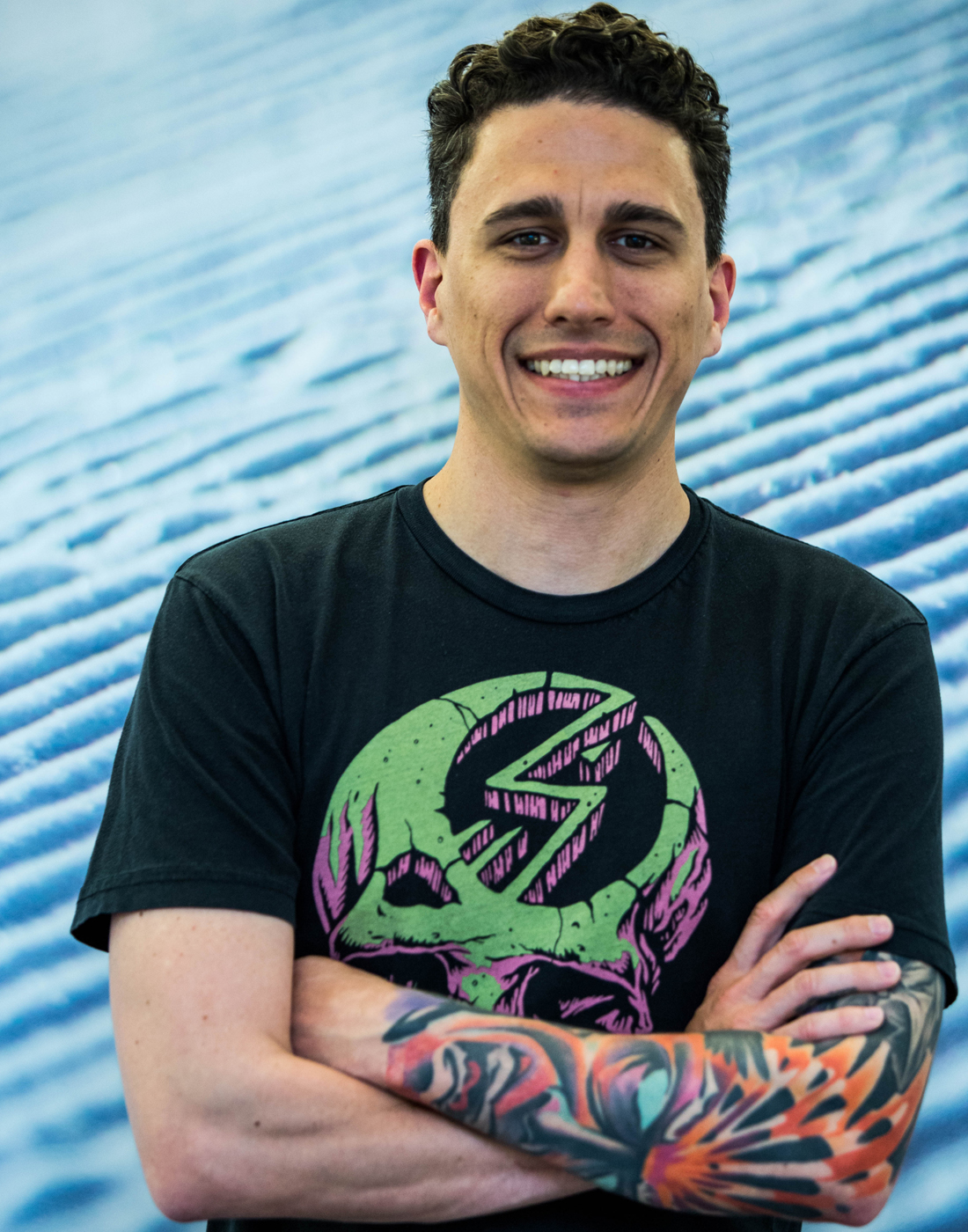
Now, let’s broaden the spectrum of this conversation a bit. What are some of the things people really don’t know about ski boot construction?
One of the things that throws people for a loop when they start talking about how ski boots are made is just the insane cost behind bringing a ski boot to life. When we launch a new ski boot it costs roughly 1 million Euros just development costs to get a ski boot on the table in front of us—and that’s at the low end. Half the time, or most of the time, it’s closer to 2 million Euros depending on the complexity of the molds. Before we get a boot to market, we’ve already spent over [that amount]…. it’s one of the things that ski-manufacturing side has a little bit easier; it’s also why you can see a lot of smaller, indie, garage brands in skiing, but you’ll never see it in ski boots.
How many people are involved in the process of that idea to put it on the table?
A lot of people are involved in bringing this to life, sitting here in Altenmarkt, Austria, is the full R&D team behind Atomic ski boots—it’s about ten or eleven people that are responsible for bringing the ski boot from idea to finished product.
And beyond that, putting them on the racers and the athletes…
Oh yeah, getting them into the market is a huge, global [effort] that I couldn’t even begin to count. But, when we develop a new ski boot, especially a boot like the Hawx Ultra XTD, it’s super crucial to have our athletes involved from day one. Guys like Sage [Cattabriga-Alosa] and Chris [Benchetler] have been super instrumental in helping bring a boot like the Ultra XTD to life, making sure it meets their needs from the very start, as well as the consumer’s [needs]. Without them, it would be definitely harder to hit the nail on the head.
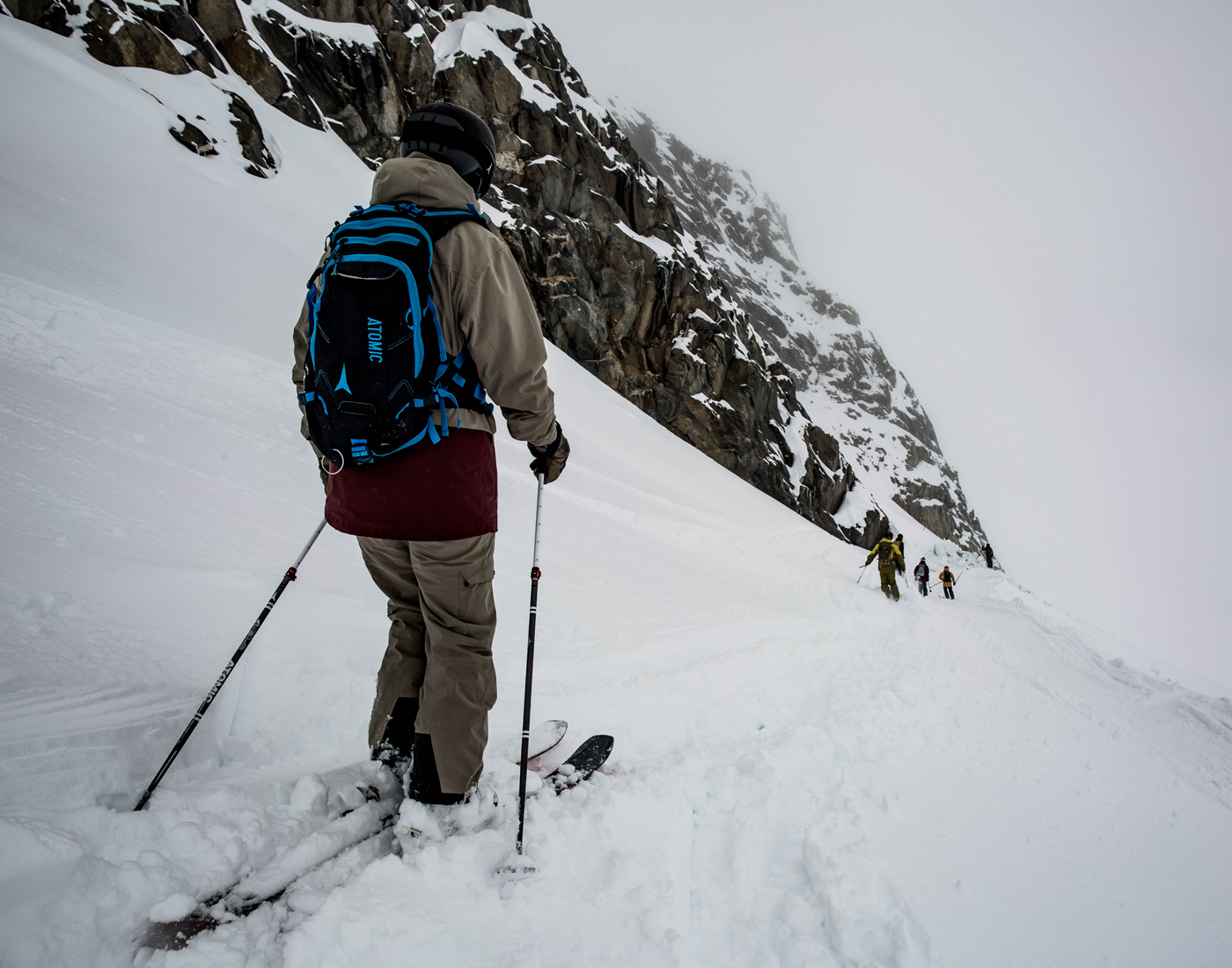
More generally, what is the most important thing for a consumer to consider when buying a new pair of boots?
When people are buying a new pair of ski boots, they should always have at the forefrontL fit, fit, fit. Finding the right fit is, by far, the most important thing about a ski boot, and by “fit” I mean the right size for your foot, the right shape for your foot and your leg. What people should really focus on is researching who are the best boot fitters in [your hometown] or at your local ski area, going to them, making an appointment and blocking an hour of your time to really sit down with somebody who can look at your foot shape and analyze it to best match it to a ski boot.
Lastly, and also of utmost importance, footbeds are super important. We think every skier needs a nice aftermarket footbed, one that is built for their foot, supportive of their foot in the right way.
Lastly, in your opinion, what sets Atomic boots apart from the rest? As a designer for the brand, what keeps you excited about the product?
Looking at the three things we focus on when making a ski boot—fit, comfort and performance—I would say that all the other brands would probably say the same. If you’re making a ski boot and you’re not focused on those three things, you’ve missed a huge portion of what a ski boot ought to be. It’s fair to say that every other brand is focused on those three things but what makes Atomic stand apart from those are our solutions to them; most notably, and currently, that’s Prolite. For thirty years, ski boots have been pretty heavy, made of thick plastic—in some aspect, boots will always be built that way—but we’re the first brand to really challenge that construction and bring a boot to market that’s… lighter but still has all the skiing performance that an all-mountain consumer comes to expect.